Met een slogan als innovate or die moet je altijd vooruit kijken. Het is niet voor niets dat in Morgan Hill een heel leger van wielergekke rondloopt die zich 5 dagen per week bezig houden met de toekomst van de wielersport. Grote kans dat ze die andere 2 dagen in de week zelf op de fiets zitten.
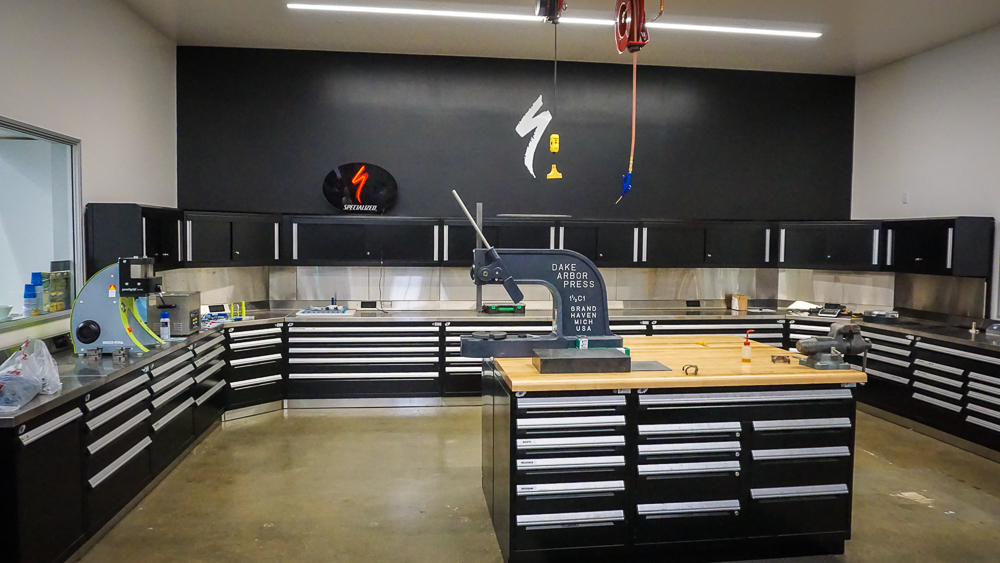
We nemen een kijkje op de gigantische R&D afdeling. Daar waar de deur normaal gesloten blijft mogen we door. De afdeling bestaat uit 6 verschillende ruimtes. De grote centrale hal is de werkplaats. Wanneer er digitaal iets bedacht is en dit moet worden getest dan kunnen er in huis prototypes worden gemaakt. Dit kan om allerlei verschillende zaken gaan. Van het frezen van een klein onderdeel als een link of derailleurpad tot het lassen van complete prototype frames of custom made carbon wielen.
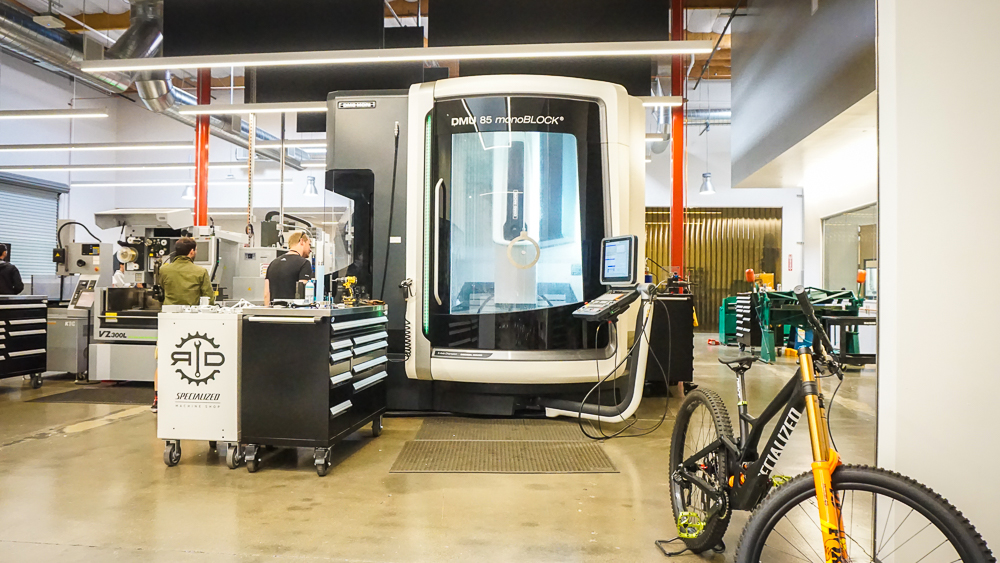
In de hal staat een gigantische freesmachine. Het apparaat is zo groot als menig total werkplaats en schaaft in sneltreintempo een groot stuk aluminium tot fietsonderdelen. Niet alleen prototypes worden hier gemaakt. Ook veel speciale onderdelen voor één van de vele door Specialized gesponsorde remmen worden hier gemaakt. Denk bijvoorbeeld aan op maat gemaakte suspension onderdelen voor het downhill team.
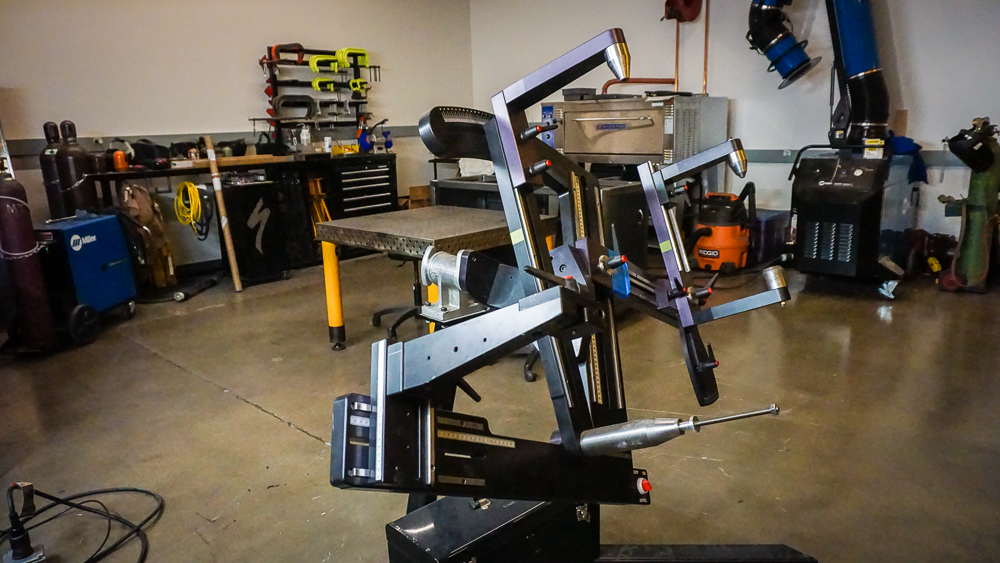
Frames op maat lassen? Geen probleem.
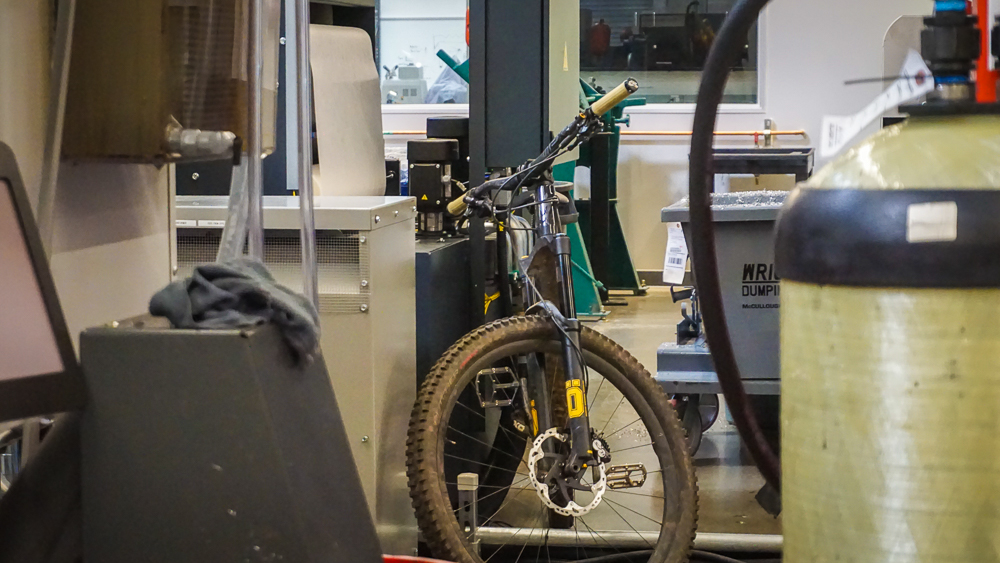
Overal staan fietsen.
In het Carbon LAB wordt in sneltreinvaart gewerkt aan het ontwikkelen van de volgende generaties frames en onderdelen. Een eigen snijtafel. Meterslange rollen materialen en rekken vol met mallen vinden we terug. Dan Lister, Tech manager op de carbon afdeling laat ons allerlei verschillende productiemethodes zien. We krijgen meer inzicht in hoe zo’n frame tot stand komt en waarom een carbon frame zo kostbaar is.
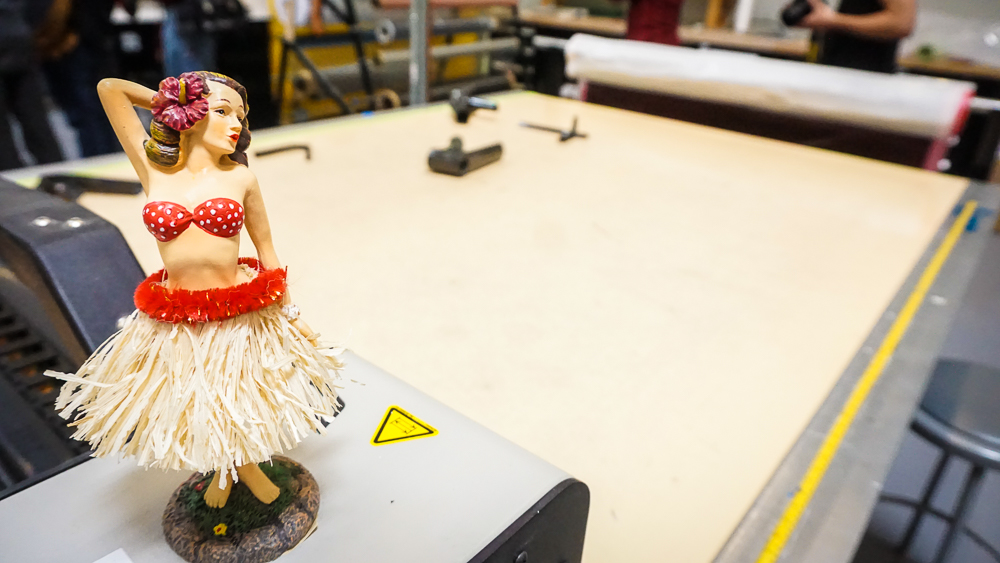
Eens kunststof mal dient als basis voor het frame. Deze krimpt later in de oven zodat deze verwijdert kan worden.
Mallen frezen doet Specialized in eigen huis. Zo liggen de kosten relatief laag en kan er eindeloos worden geëxperimenteerd.
130 ‘onderdelen’ en meer dan 30 verschillende soorten carbon vormen samen een frame. Het ‘opbouwen’ van een frame inclusief het bakken ervan neemt zo’n 8 tot 9 uur in beslag. Morgen kijken we verder. Dan lopen we door naar de ‘WinTunnel’ Specializeds, eigen wintunnel die dag in dag uit draait om nagenoeg elk product efficienter te maken.